- China declara que “ignorará” los “juegos de números arancelarios” de EE.UU.
- Beca PERUMIN: Más de 2180 jóvenes de 23 regiones del Perú postularon para acceder a las actividades de la Convención Minera
- Minem: el Algarrobo es el primer proyecto en priorizar el recurso hídrico en Perú
- MINEM: Cusco será la primera región del país con proyectos en energía rural trifásica
- Impulso a la equidad de género resaltó en Encuentro de Mujeres Líderes de Ferreycorp
Evolución y performance capacidad volumétrica para equipos cónicos
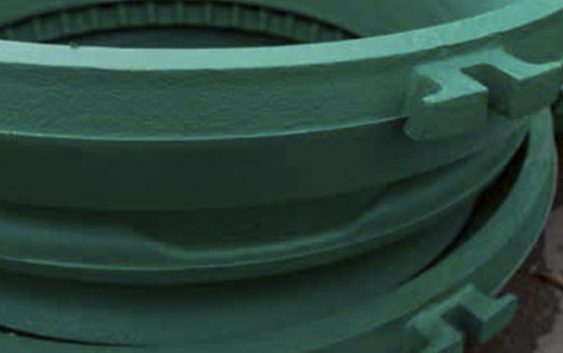
Para alcanzar la mayor eficiencia en las operaciones de equipos cónicos, es esencial definir el momento adecuado de retiro de las piezas de desgaste y entender los cambios en el material a medida del uso.
Dentro de las operaciones de equipos cónicos, siempre se busca trabajar con la mayor eficiencia posible, es decir, conseguir la mayor productividad y el aprovechamiento máximo de los revestimientos de chancado. Para ello, es esencial definir el momento adecuado de retiro de las piezas de desgaste, y entender que a medida que van desgastándose los revestimientos, van ocurriendo cambios en la capacidad volumétrica. Parte del soporte de Metso Outotec es ayudar a identifica el momento adecuado para conseguir un equilibrio entre tonelaje por hora procesada y aprovechamiento máximo de las piezas. Por ello, en este artículo se desarrollarán los factores a tener en cuenta para maximizar la eficiencia e este ámbito.
“Es importante evaluar si el continuar utilizando revestimientos por encima del 50% de T.U. compensa la pérdida en TN/hr que se generará”.
Diferencia entre cavidad nueva y desgastada
A continuación, se podrán apreciar dos imágenes. Ambas muestran un corte transversal de revestimientos de chancadora bajo dos condiciones: a la izquierda se muestra el perfil sin desgaste (nuevo) y a la derecha, el mismo perfil desgastado luego d trabajar cierto número de ciclos. El perfil desgastado presenta espesores tales que se encuentra por encima del 50% de utilización, por lo que se estima que fue retirado en el momento adecuado. Nótese que ambos perfiles mantienen el CSS en 40mm de diámetro, pero sin embargo el top size 112 ubicado en el perfil nuevo, en la cavidad desgastada se ubica fuera de la zona de chancado, la medida del top size de la cavidad desgastada cambió a 84.
Para poder graficar mejor la capacidad volumétrica (en 2D), esta se resaltó en ambos perfiles, donde se puede visualizar que ocurre una disminución en el perfil gastad. La cavidad, al tener una menor capacidad volumétrica, procesará menos toneladas por hora comparado a una pieza nueva. Esta comparación es necesario hacerla al mismo CSS (en este caso es 40), ya que, si aumentamos el CSS del perfil gastad, se podría recuperar la capacidad volumétrica, decayendo la calidad del producto.
Performance y productividad del perfil
La etapa de productividad del perfil a lo largo de su vida útil está comprendida por 3 fases:
– Fase inicial
Se ha logrado observar que la mayoría de las veces, los revestimientos nuevos inician en un 80% de la capacidad productiva. Esto se mantiene por un breve periodo de tiempo mientras ocurre la adecuación de la cavidad a la condición operativa.
– Fase intermedia
Esta fase inicia una vez que el perfil está adaptado a la granulometría, CSS, tonelaje y hay una estabilidad de los parámetros operativos dentro de los rangos de seguridad. Este periodo se mantiene cerca al 100% de la capacidad productiva por un periodo de tiempo mayor al anterior.
– Frase decreciente
Se ha estimado que esta fase se alcanza una vez que el perfil d desgaste alcanza un 50% de consumo en peso. En esta etapa es donde se recomienda realizar el cambio de revestimientos, debido a la reducción de la capacidad volumétrica, lo que desencadenaría un decaimiento acelerado de la amplitud productiva.
Recomendaciones finales
– Mantener un registro histórico de los pesos de las piezas gastadas para poder obtener la tasa de utilización, lo ideal es estar entre el 45% y 55%.
– Tener en cuenta la fórmula para calcular la tasa de utilización:
– Mantener un monitoreo de producción de TNs/hr.
– Identificar cuanto decae el TN/hr al alcanzar el 50% de tasa de utilización. Si este valor se encuentra por encima del 10% de pérdida de TN/hr, se recomienda realizar el cambio de revestimientos.
– Es importante evaluar si el continuar utilizando revestimientos por encima del 50% de T.U. compensa la pérdida en TN/hr que se generará. Esta pérdida en tonelaje es compensada inmediatamente si se decide cambiar por revestimientos nuevos.
Allan Ponte
SALES TEAM LEADER CRUSHER WEARS
METSO OUTOTEC